History
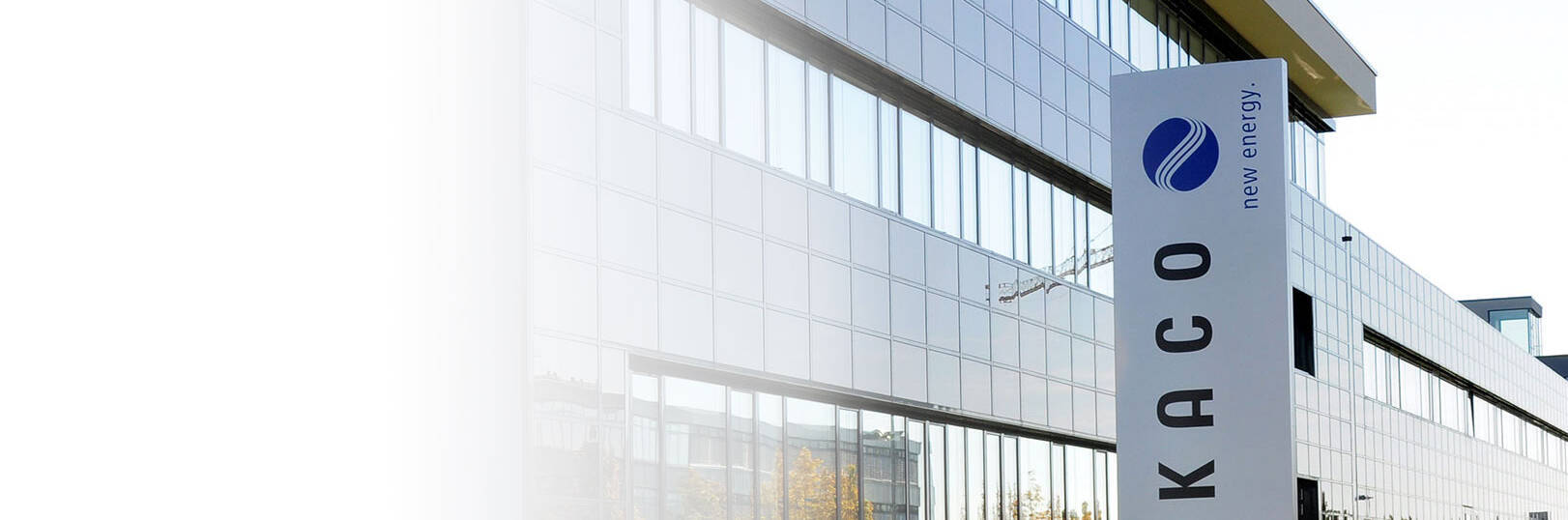
We turn passion into power
KACO new energy, as a medium-sized company with dedication and a passion for research, stands for high quality engineering skills in the field of independent and decentralised energy supply. Our inverters are designed to support the use of renewable energies as well as efficient energy management throughout the world. We implement projects with quality and commitment, and develop our products continuously.
A Siemens Company
We are committed to digitalisation in the power supply industry, integrating solar PV into various sectors and are thus actively shaping the energy world of tomorrow in different countries. Since the end of April 2019, KACO new energy has been a subsidiary of Siemens AG.
Within Siemens AG, KACO new energy is the specialist for power electronics for decentralised energy supply. As part of the Operating Company Smart Infrastructure, we benefit in particular from the exchange on topics such as building technology, electromobility and energy storage.
Who we are and where we come from
Click the following categories to learn more about our foundations, the values that define us and how the company is run accordingly.
Sign up for our free Newsletter
Keep up-to-date with our regular newsletter:
It informs you about new inverter solutions and latest projects, ways to efficient energy management and important industry updates.